Whats in a name?
- acolltobuild
- Jul 19, 2024
- 17 min read
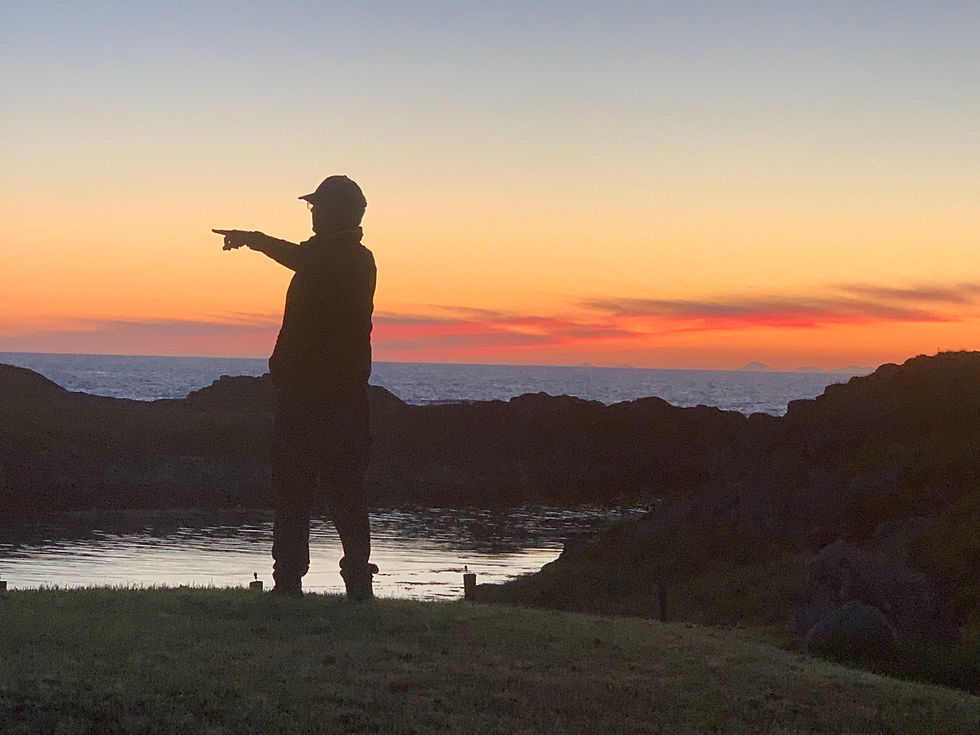
So what is in a name? Well, we have been thinking of a name for the house for a long time now and, until recently, had not come up with anything that felt quite right. We feel that naming a rural house, which will one day appear on a map, carries a certain responsibility. It should not be anything to do with us but to do with the land. It needs to be timeless - relevant in the past and in the future. So we've been looking for inspiration along those lines. There is a profile of a giant head on the ridge behind us which is not named nor referenced on any map. It is a remarkable rock feature which has existed at least since the last ice age and, unless something very bad happens, should be around long after we are gone! So for a while now, that has been the focus for our name searching. Landmark names on Coll are predominantly gaelic but there are also a good few viking references. For example, close to us we have Cornaig Beg and Cloiche (gaelic) but also Sorisdale and Bousd (from Viking/Norse origins). We felt gaelic was right for a name and are aware that it is easy to make a linguistic mistake as certain gaelic words don't work together. So we would need some help!
This is a photo of the head framed by our caravan window...
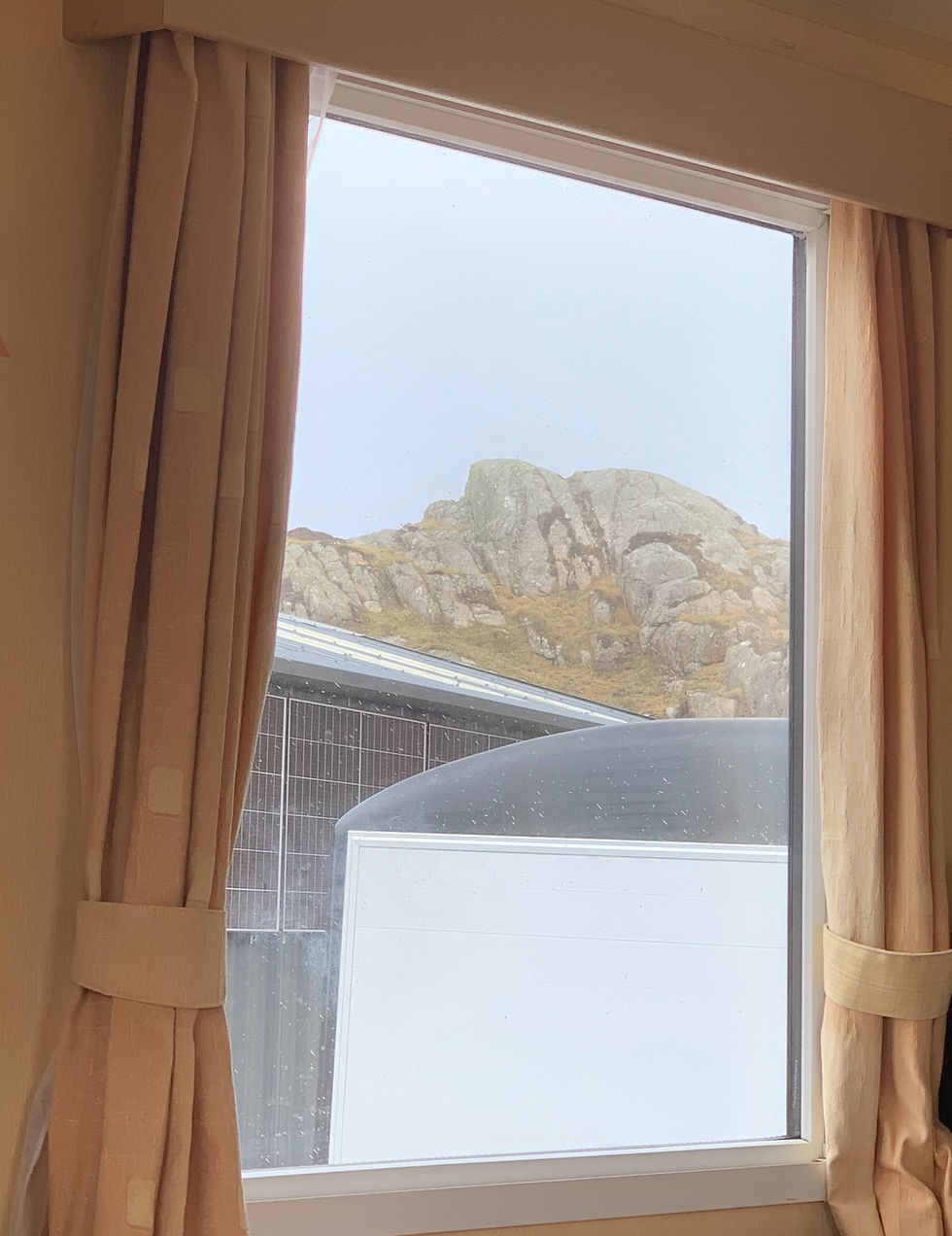
We have kept open minds on this idea though as finding gaelic words that work (and gaelic words that our southern pals could actually pronounce correctly) might have been difficult!
Kirsty, who lives up the road is a gaelic teacher and also very knowledgeable on the island history and she very kindly offered to help. We were invited round for a coffee to discuss both gaelic names and the local history. Kirsty had dug out a lot of old maps and history books which were really interesting and we threw ideas back and forth for a while considering water courses, march boundaries, old settlements and any other feature close to our plot.
One of Kirsty's old maps...

Traighs Bhorbaidh on this map is a hill fort just behind the ridge with the giant head on it. It is an ancient hill fort on the shore with little to see today other than circular scars where the ground has been sculpted. This map is only one name source and Kirsty's best guess for the original gaelic name actually translates to "Fort Fort" which wasn't that inspiring. We did establish however that it was occupied by vikings at certain times. During the chat, we also learned that the gaelic word for Viking is "Lochlannach" which literally translates to "the people of the land of the lochs". We liked this! It is how our gaelic ancestors described the vikings because they hailed from the Norwegian fjords. With some poetic license, we now refer to the nameless feature on the ridge as "the big viking" which translates in gaelic to An Lochlannach Mor. And that's what we have decided to call the house. No doubt locally it will be abbreviated somewhat... maybe something like Lochy Mor or just Lochlannach.
The three of us were very happy with this and Kirsty reached for the whisky to celebrate with a dram. A thoroughly enjoyable and satisfying visit. Thanks very much to Kirsty! We've now registered it at the post office so if you put our post code in PA78 6TE, you can find it (although it's not located correctly on their map yet)!
So, on to the project itself. There's no point in having a name if we still haven't got a house...
We have decided that all non essential outside work is banned until further notice. We are inside all the time come rain or shine to try to finish enough of the house so we can move into it! The outside stuff, which is what we much prefer, will have to wait for now. Our friend Clive, who has a lifetime of experience running complicated projects, visited us last year and he had stern words about the lack of a project plan. So, before we returned in the spring, we created a detailed plan which "said" that if we applied ourselves to the right tasks, we could finish the upstairs by the end of summer. Upstairs by the way, includes a bedroom, a snug/tv room and a bathroom so it would be great to have this done before the winter sets in.
The plan is VERY long but here's a small extract to give you an idea...

So even in glorious weather, you'll find us inside, mostly working on our knees which unfortunately aren't in very good shape... Julia had a ski accident in March (it's normally me but this time Julia took a tumble) and she severed her ACL amongst other things. She has borrowed a turbo trainer (thanks Brian and Fra!) and set her bike up in the garage for physio.
I have a far less serious "bursitis" which I think is the medical name for what used to be called "housemaid's knee". You probably can't say that these days! Anyway, the good news is we are both able to work to a point and walk around and Julia can still go for her daily "fix" swimming in the freezing sea. I am unable to kneel on my bad knee which is limiting but can normally find a way of getting things done. Sometimes I think we are a bit old to be taking on this project but it's a little too late to worry about that now. Age, strength and injuries slow us down but it's still just about manageable. My advice for any over 55 non builder who wants to take on a house should probably plan for about 30% "down time".
Here's a photo of Julia's knee (she let herself go a bit and isn't shaving much these days) ...

So injuries aside, what have we done since the last blog? Well quite a lot really. In spite of being away for more time than we should, I'm pleased to say that much progress has been made. We said in the last update that our focus would be "infrastructure". Infrastructure is mostly done now, with all the plumbing installed and tested where possible. This obviously doesn't include installing plumbing appliances (like taps and baths etc.) but the pipes arrive where needed, they carry water, and are tested ready for connections.
The pressurised plumbing has been tested to a minimum of 3 bar so hopefully all leaks have now shown themselves before the pipes are hidden away by plasterboard! We did have a few leaks, both with the push fit plastic pipes and the copper welds. The best connections have been the compression joints where an olive is crushed onto the copper pipe sealing it. when they leak you can normally stop it by simply tightening the nut. If I had the time again though, I would have pressure tested them all with more than just my party balloon system - especially the ones from the stove to the thermal store which are under the floor now. Fingers crossed they don't leak. This is unlikely though as they are not pressurised and they didn't leak for the first 2 weeks when exposed.

Once we finished the underfloor heating (which consists of nearly a kilometre of pipes), we then had to fill the voids with a dry cement mix. This is known in the industry as biscuit mix and was a slow process. I made the sand/cement mixes and Julia screeded the mix between the battens.

The manifold for the underfloor heating has been fully installed apart from the thermostatic room controls. It is connected to the thermal store and amazingly, the £12 pressure tester we bought on Ebay worked! The whole system has been tested to 5 bar.


We also installed and tested a separate circuit for the 3 radiators upstairs. This will be both heating for upstairs (which may well never be needed) but also a heat dump system if the thermal store becomes too hot. Underfloor heating won't work as a heat dump because it only circulates water to about 40 degrees. We need a heat dump because we use an uncontrolled heating source (the stove and back boiler) and can't quickly or automatically turn it down. Also, if we ever get round to installing a small wind turbine, we would connect it to an immersion heater. The electricity a turbine produces must be used somehow otherwise, if nothing is connected, the turbine will spin freely and self-destruct! When you connect something that requires power, you also create an electromagnetic "brake" for the turbine.
We have installed three super low energy circulation pumps which can be set to use as little as 3 watts so power to run them will never be an issue.
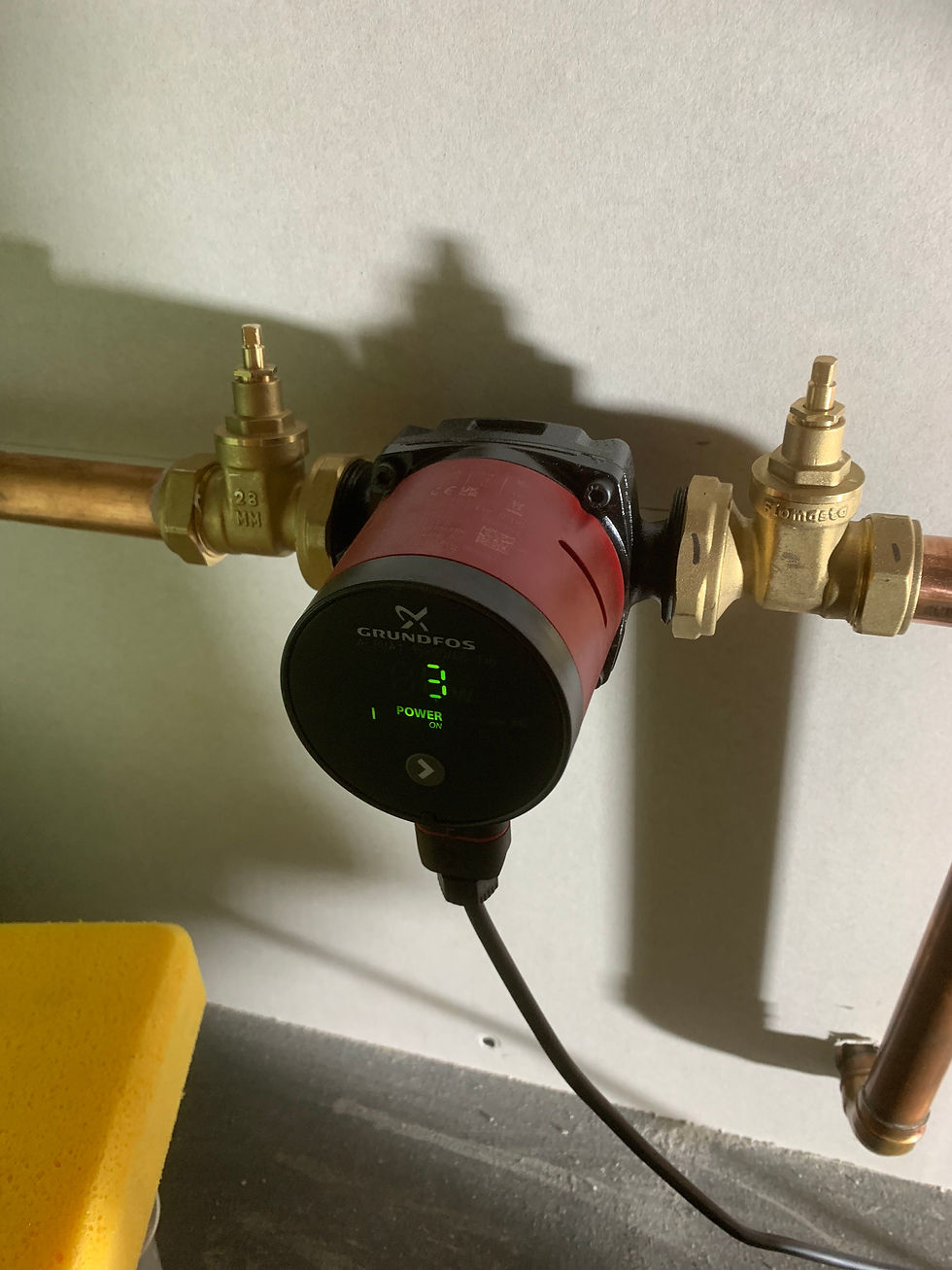
Once the biscuit mix covered all the underfloor heating pipes, we installed the flooring on top. This is T&G chipboard (Tongue and Groove). We slot them into each other and screw and glue them to the battens taking great care not to hit any of the pipes below! Despite carefully marking where pipes crossed the battens, we (or more accurately, I) still very nearly hit one.
We've done about 90% of the flooring but are leaving some of the low priority rooms just now to focus on the upstairs work. At some point in the future we will lay the LVT flooring on top of this.
We were waiting for the perfect weather window to put the stove chimney through the roof and the Gods delivered! 2 perfect winter days and it was done. It was a very stressful experience though. Not just because of the height but also because once you have cut a huge hole in the roof, you need to cover it with a flashing before the next downpour. The flashing we had was only just big enough and getting it over our high roof profile (the peaks and troughs in the metal roof) was no easy task. Anyway it is done, and we have installed a special insulator sheath to bridge the gap between the flue and timber structures. There has to be a 50mm gap between the flue and combustible materials. Many houses have uninsulated voids between the chimney and the insulation which is the cause for a lot of heat loss.


So now the stove is ready to be lit! We haven't actually got round to firing it up yet but will do very soon.
After all of this, we turned our attention to the upstairs. We have finished the vapour control foiling now but with many innovations needed. The house should have been constructed with the vapour control layer on the inside of the external walls right up to the ridge beam. For that to work the VC foil needed to be put behind the internal walls and around the top of the ridge beam. This was not done so we are now required to try to fix it across the internal upstairs ceiling. This means we need to try to seal it around all the pipes and wires that run above the ceiling. This is a lot of extra work and is not likely to be as airtight as with the intended design.
We also installed the MVHR system (mechanical ventilation heat recovery). This is a large box of magic with sealed air ducts running in and out. There is an individual duct going to every room. It draws out the stale air from the kitchen, utility and bathrooms and blows in fresh air into the bedrooms and sitting room. The clever bit is that when it expels the heated stale air, it converts the heat into the cold air being drawn in from outside. 87% of the heat is recovered.
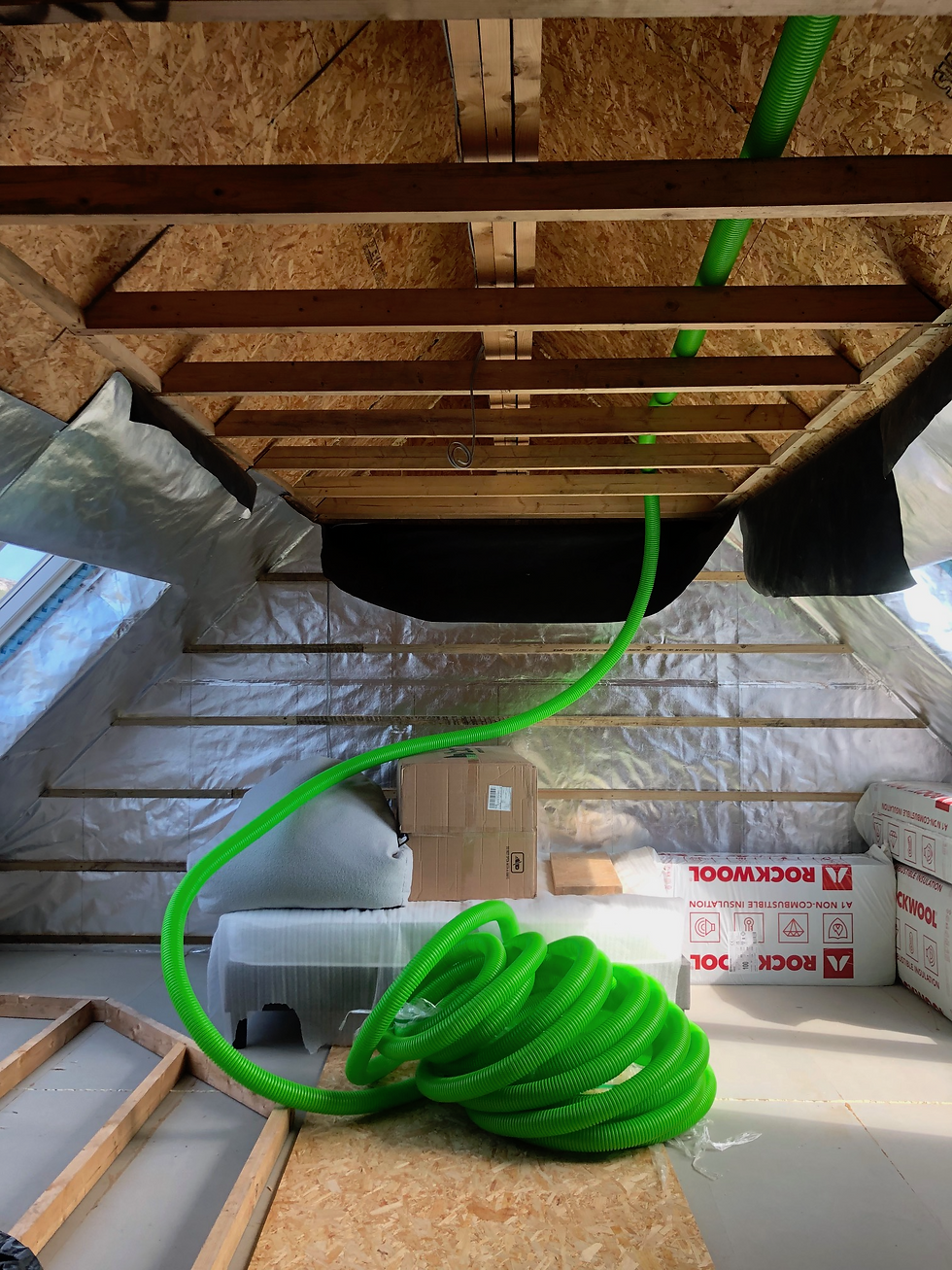
We have put the unit and manifolds under the eves where we have built a cupboard just big enough to house it...

As there are a considerable number of wires, pipes and ducts in the upstairs ceiling void along with our header (F&E) water tank, we built a crawl board to allow access for the whole length of the ceiling. There will be 2 ceiling hatches as a central wall divides it in two. Again, its very hard to seal the foil with an opening hatch, however we have found a company called Jupiter Blue (@jupiterblueltd) who provide air-sealed hatches. They have been really helpful and we are now in receipt of 2 airtight hatches. The openings are made and we are ready to install the hatches once the plastering is done.
This is a very big drill to make a very big hole for the external duct...
So, once the VC foil and MVHR was installed we were ready to start on the plasterboard. We have now completed all the plaster boarding upstairs which was extremely fiddly with lots of awkward angles. We had the help of a gadget which lifts and holds sheets up so they can be fixed without having to bear their weight while screwing them on. We bought it second hand from someone on the island and it has been essential. We have also been lent a plasterboard screw gun by one of our neighbours (thanks Steph!) which has also been really helpful.
A special platform was required to get to the area above the stairs...
The plasterboard needs to be fixed on all sides and level so there has been a hell of a lot of "dwanging" and "shimming" involved. Dwanging is the placing of extra wooden battens to support the sides of the plasterboard where no stud/timber exists and shimming is the process of filling a gap with a spacer to make a level surface. It's often necessary to cut (and then waste) plasterboard if the timber stud work design does not comply with the standard sizes of plasterboard. There is a design process called "value engineering" whereby a house is designed to avoid waste and utilise exact sizes of materials like plasterboard. Unfortunately the upstairs of our house is not "value engineered". Had the panels and partition walls been designed with regular gaps and had they been joined together level then a lot of this could have been avoided. We live and learn! Had we known what we know now we would have paid attention to the detailed designs at the outset and we would have checked all the delivered panels and installed walls to make sure they complied. Oh well!
This is what dwanging and shimming looks like - bringing the wall level for the plasterboard to be screwed on ...
Once the plaster boarding was done, we turned our attention to door frames. This is a very tricky job, not helped by the lack of plumb and level walls. Some of this is our fault and some of it is down to the kit partitions that were supplied with "rhombus" doorways! You have to get them level in 3 dimensions and once again pythagorus was used to make sure the frames were held square before installing them. If the door frames aren't right, the doors wont fit well and they will swing open/shut.
Due to the varying width of the openings, we had to cut the wood to size and make our own frames. You can buy standard pre-manufactured ones but once again, it depends on the standardisation of the structure. Lucky for us Matt, (a Cornish carpenter who has relocated to Coll with his girlfriend Tasha who is the daughter of farmer Rob), was on hand to show us how it's done. We also had an exploding table saw (which is the vital tool needed to cut or "rip" wood along the grain). Matt brought his saw up and we managed to cut all length needed. His visit turned into a spontaneous night involving supper and most of my whisky supplies which was great fun. Thanks again Matt!
All 6 of the upstairs frames are in place and hopefully good enough to hang doors on!
We always knew that plastering was the one thing that is "above our pay grade" and we planned to engage a mainland professional to come and help us. Before doing this we thought it prudent to ask Pete, a retired plasterer who has one of the most idyllic coastal houses on the island, to visit us and check that the quality of our work was good enough for a plasterer to perform their magic. Pete came over and to our surprise, he offered to help us so we have now started the plastering thanks to him. Its a full on job and much harder than I could have imagined. What Pete does is really amazing and we are so grateful that he's helping us.
Two of the 3 radiators have been hung as well but we haven't connected them yet as they need to come off the wall for the plastering. This was me checking the strength of the fixings...
And the mounted radiator (note the use of plasterboard off cuts behind!)...
So the upstairs plan is going well. We have bought all our bathroom furniture, fittings and tiles and we will make a start on that shortly. A huge thanks to Doug McD and his creeking van for lumbering it all up from Edinburgh for us! We hope the next blog in the autumn (?!) will have a few shots of the upstairs in a very near finished state.
Apart from the house internals, there are a few other updates. We decided to install an alkalising filter on our water supply. The Ph of rainwater is about 5.9 which is a bit low. Acidic water isn't bad for you but it is bad for copper pipes and as we have a copper heating coil inside our thermal store it makes a lot of sense to increase the ph. Its now at about 8 which is fine. The crystals in the filter needs to be replenished every couple of years but it is only about £20.
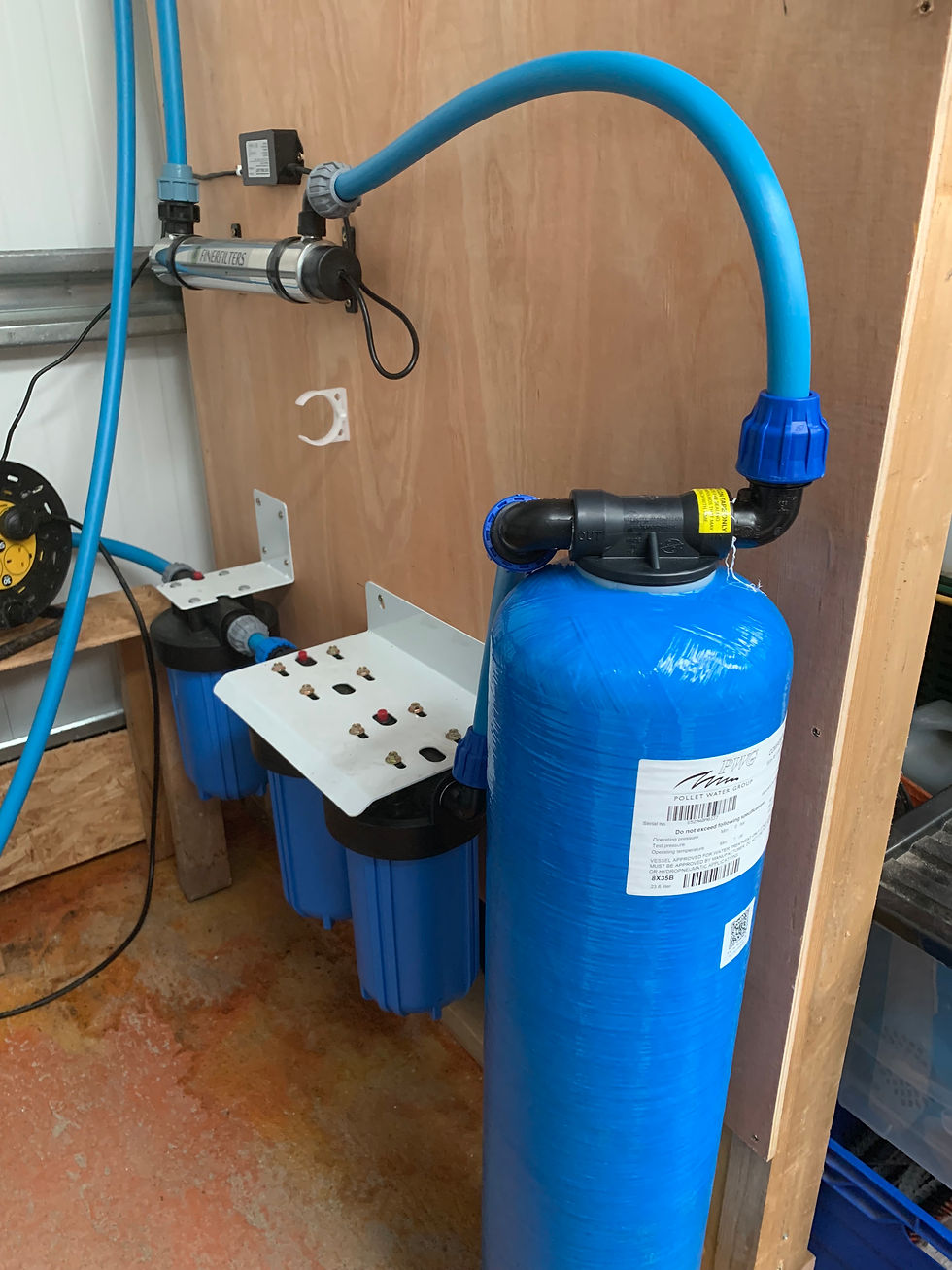
In general the water supply has been working really well. We have not had any worries about running out and frankly if there is an extreme drought in the summer it means that we are having amazing weather so what the hell! We can ration water if need be and our 11,000 litres would last months. The lowest we have been was about 6000 litres after 48 days of no rain last summer. And, all it takes is one good rainfall and we are once again full!
The pond could be a contingent source of water however we do not intend to use it for that unless our supply is compromised somehow. The pond has remained full during the summer with a constant flow in and out. The water comes through the ground from the adjacent high ground (underneath the big Viking) and sits in a natural sump between bedrock. Once we dug it, even in the drought of last summer, it filled itself in a few days. It is not lined so all we have really done is to dredge a natural sump. I am also pleased to report that at least some of the 6 trout I caught and put into the pond have survived. At least 2 of them have been rising for flies so they have over-wintered living on the natural habitiat. They may breed but we think not due to a lack of water flow and gravel bed. If they don't they will get a lot bigger and I might have to get the fishing rod out...
There is less good news about Julia's trees. Initially they were growing really well but a vicious 50mph northerly wind seems to have all but killed them off. Most of them are still showing signs of life but we were shocked to see how devastating the wind can be to newly planted trees. We need to create a complete wind break area in which to plant things. I suspect this will be a combination of landscaping and wall building but we have no fixed plans yet.
On the positive, the grass is growing well and we soon won't have any sand left around the house. We've also had some nice flower blooms over the summer. Both ones that Julia planted and wild flowers.
We already have the polycarbonate sheets we eventually use to build our Polytunnel. This will be along the lines of a Polycrub (an Orkney manufacturer of storm resistant poly tunnels) and will be a lot sturdier than a polythene one and more suitable for the Coll "breezes". One thing that is needed for this is about 90 meters of thick PVC piping to make the structural hoops. As luck would have it we got wind that a of a long run of such piping had been washed up on the shore in a remote part of the island. We managed, with some considerable effort, to recover it from the sea at low tide and cut it into 10m sections. We recovered 150m in the end - enough for 2 big poly tunnels. This was an excellent day's scavenging and probably saved each of us about £800 as this type of pipe ain't cheap!
Rob and Alex helped take the cut pieces off the rocks and drag them back to the road...
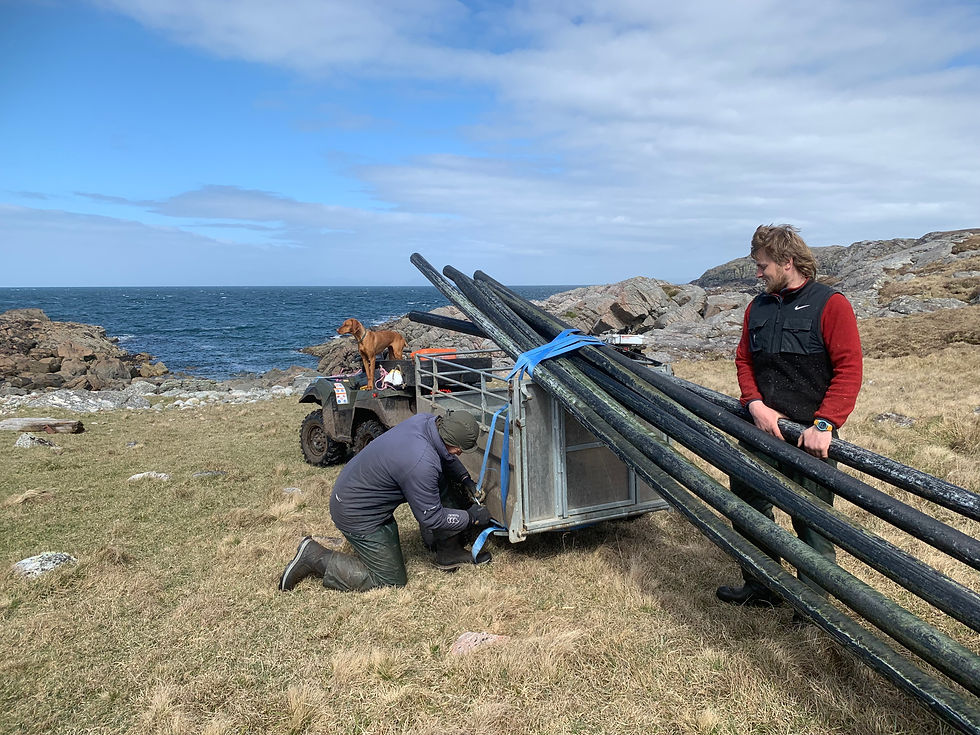
I then used the quad to take our share home...
Julia has also been publishing instagram post on our project (@acolltobuild) and put a reel up of my journey on the quad. For those old enough to remember, the music is from the rather dated Benny Hill Show... where are the scantily clad ladies though?!
There are three outside jobs that need to be done this summer in spite of our plan to stick to the internal works. After 3 years of use, the track up to our plot is now in need of some attention. There have been a lot of heavy loads going up but oddly it's not them that have caused the major damage. It is 2 wheel drives that get so far up and the wheels start to spin digging deep ruts and generally churning it up. We are planning to lay a couple of reinforced concrete runners on the steep section to help the 2 wheel drives up without wheel spins. Lets hope that works. We also need to re-stain the cladding on the SW side of the property. This has been damaged by wind/sand blow and in order to protect the wood, it needs another coat of stain. Crazy after just 2 years! And lastly, we need to put lock nuts on the solar array to ensure panels are well fixed in the winter storms. If time permits, and and we are blessed with an Indian summer, it would also be nice to lay the patio stones.
As far as the house is concerned, once the upstairs is done, we need to turn our focus to the kitchen. As there is an inevitable lead time with deliveries, we will need to order it soon!
So in other news, we've had a few visitors this summer starting with my now 91 year old Mum along with my sister, Gill and her husband Chris (the engineer who advises us on all technical queries!). Gill's friend Linda also came along so it was quite a gathering for our wee caravan! Mum and Linda stayed in the storm pod half a mile up the road though so it was fine. Unfortunately the weather was a bit mixed and very cold but we managed a few walks.
We then had a long awaited visit from Julia's long time pal from Ireland, Mairead with her husband Simon. It was great to finally show Mairead and Simon the island and what we've been up to. The weather was mostly ok and to Julia's delight, both of them went for a swim in the freezing sea. They sensibly booked the hotel for their visit so did not have to experience the full rigours of caravan life. Simon, Nick and I went fishing on the South shore (due to the Northerly winds) and returned with a couple of nice fish for supper.
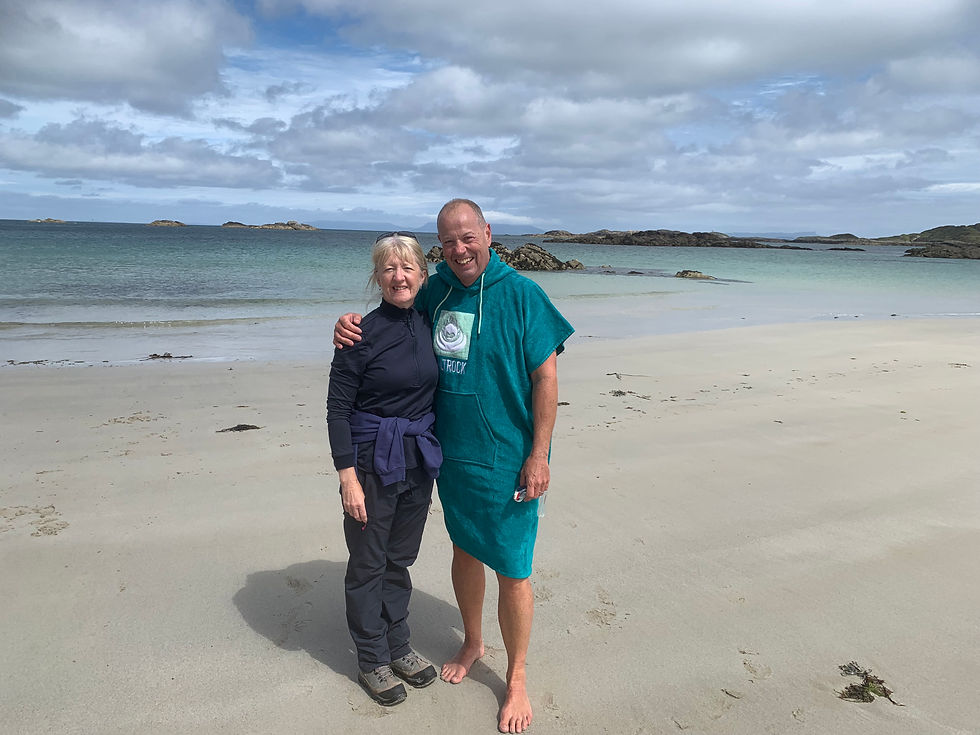
Neil also made a trip out here and is one of our most frequent visitors in spite of living in Geneva. For that, he gets to feature on the cover shot. Yes, it is he pointing in the sunset although we've no idea what he was pointing at! Neil was returning from Benbecula were he grew up and where he had returned to scatter his parents ashes. It turned out to be a rather difficult journey in spite of it being only a few miles away across the sea. He helped me build a platform that can go on the stairs for plastering/plaster boarding access...
The last visit was unexpected. Ronnie, who has visited us a few times before, was sailing his yacht somewhere between Ireland and southern Scotland when he received the sad news that one of his cousins had died suddenly on the Isle of Skye. The funeral was just 2 days away so Ronnie phoned me asking if I could kit him out with a suit, a white shirt, a black tie and some formal shoes. If so, he could stop in Coll on his way North and then head directly to Skye for the funeral. As luck would have it, I was able to kit him out with a surprisingly good fit too. He stayed on his boat but we all went to the hotel for dinner which was great. Apparently my funeral attire is now somewhere in central Scotland and due to be delivered back to me in September. I also learned that his full gaelic name from Skye is "Raul, Raul, Shaunie mac a Hamish" a slight improvement on Ronnie MacDonald!
Island life has been good as ever and there is always plenty going on. We have recently been blessed by presence of Barbara Dickson, Ally McBain and Phil Cunningham who came to perform a concert for us. This was thanks to Rob who somehow managed to press-gang them into a charitable visit. The music was exceptional and everyone really appreciated them coming.

We have a few big events coming up soon too. There is a big birthday celebration in September (someone's going to be 60 ...eek!) and the Doddie Disco on the 28th September which I'm sure will be a great craic. Tickets are still on sale if you are interested!
Here's the link... https://www.doddiediscofest.co.uk/
And finally, some of the frozen swimmers popped round after their "dip a day in June" to celebrate builder no1's third caravan birthday...

So that is the round up. A bit technical and boring but at least a record of our endeavours.
Next update in the autumn. In the mean time we wish you a well for the rest of the summer!
Keith & Julia xx
Great update Keith, what a journey and new set of skills you've both acquired along the way. Finally found the house on Google Maps using Kirsty's old map and clues in your search for a house name. What a great location. Love the trout farm! Hope to catch up in '25 or '26. Cheers Chris
Wow, thanks so much for the update, Keith. It is coming along really well. Hope you guys are doing the same :). Also, really love the name. All the best, Noah & Lydie
Brilliant, especially when no previous building experience!
Fantastic as ever. Amazing effort and such a lot of hard work xxxx